Materials & Chemicals
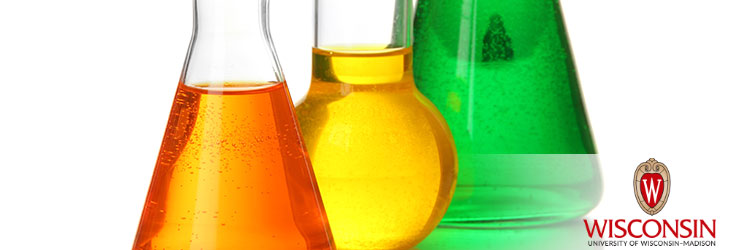
Semi-Solid Forming of Metal-Matrix Nanocomposites
WARF: P05344US
Inventors: Xiaochun Li, Lih-Sheng Turng, Michael DeCicco
The Wisconsin Alumni Research Foundation (WARF) is seeking commercial partners interested in developing a method of incorporating nanoparticles into a semi-solid casting process.
Overview
Semi-solid casting (SSC) is a high-integrity die casting technique, wherein metal is injected into a mold cavity in a semi-liquid/solid state with a “slushy” consistency. Semi-solid metal has lower energy demands and less porosity, is more easily handled and requires less post-molding machining than metal cast using high-pressure die casting; however, it is difficult to generate the globular microstructure (globular solid particles suspended in the remaining liquid phase) needed for SCC.
The Invention
UW-Madison researchers have developed a method of incorporating nanoparticles into a semi-solid casting process, so the resulting metal-matrix nanocomposite has the appropriate globular microstructure and improved mechanical properties. The metal-matrix nanocomposite is formed by heating a metal until it reaches a liquid state and then adding nanoparticles to the liquid metal. To uniformly distribute the nanoparticles throughout the metal, the metal/nanoparticle mixture is agitated by inserting a probe that vibrates at ultrasonic frequencies into the mixture. The mixture can then be cooled, and the vibrating probe removed. When the mixture reaches a semi-solid state, it can be injected into a mold cavity for SSC.
Applications
- Formation of aluminum, magnesium or titanium parts to replace heavier steel parts in the automotive industry
Key Benefits
- Machine parts and other articles formed by this process have improved properties.
- Metal/nanoparticle mixture retains the globular microstructure needed for SSC after solidification begins
- Maintains all the advantages and efficiencies of SCC
- Use of ultrasonic vibration simplifies the preparation of material for SSC, saves significant time and energy and widens the SSC process window