Materials & Chemicals
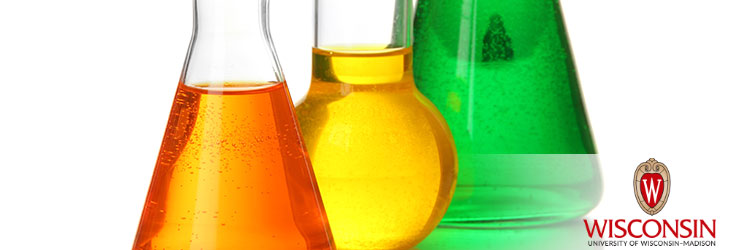
Cost-Effective Synthesis of HMF from Fructose
WARF: P06305US
Inventors: James Dumesic, Yuriy Roman-Leshkov, Juben Chheda
The Wisconsin Alumni Research Foundation (WARF) is seeking commercial partners interested in developing a cost-effective and high-yield procedure to synthesize furan derivatives (e.g., 5-hydroxymethylfurural (HMF), furfural, dimethylfuran, etc.) for use as monomers, diesel fuel precursors and fuel additives.
Overview
Increasing demand of petrochemical resources to produce the energy and chemical materials required by industrialized societies with growing populations combined with a diminishing supply has resulted in efforts to develop alternative, renewable ways to meet this need. Biomass could provide a means of obtaining both transportation fuels and valuable intermediate chemicals for production of drugs and polymeric materials if these substitute routes can be implemented in an economically feasible fashion.
The chemical 2,5-furandicarboxylic acid (FDCA) has potential as a replacement for terephthalic acid, which is used widely in synthetic polyesters such as those found in soft drink bottles. FDCA is formed electrochemically via oxidative dehydration of glucose or oxidation of 5-hydroxymethylfurural (HMF). Currently, HMF is expensive to produce due to difficult separations of HMF from the organic solvents utilized in its creation, low product yield and low HMF concentrations in the product stream. A process to efficiently deliver HMF in high yields and high concentrations would provide a cost-effective route for the synthesis of di-substituted furan derivatives such as FDCA.
The chemical 2,5-furandicarboxylic acid (FDCA) has potential as a replacement for terephthalic acid, which is used widely in synthetic polyesters such as those found in soft drink bottles. FDCA is formed electrochemically via oxidative dehydration of glucose or oxidation of 5-hydroxymethylfurural (HMF). Currently, HMF is expensive to produce due to difficult separations of HMF from the organic solvents utilized in its creation, low product yield and low HMF concentrations in the product stream. A process to efficiently deliver HMF in high yields and high concentrations would provide a cost-effective route for the synthesis of di-substituted furan derivatives such as FDCA.
The Invention
UW-Madison researchers have developed a method for the selective dehydration of carbohydrates (preferably fructose) to produce furan derivatives (preferably HMF). This new process provides a cost-effective way for making these valuable chemical intermediates, which could replace key petroleum-based building blocks used in production of plastics, fine chemicals, diesel fuel and fuel additives.
The method is more commercially viable than those previously developed because it yields a higher concentration of HMF and produces HMF in a separation-friendly solvent which does not require difficult extraction processes. The dehydration process employs a two-phase reactor system in which a reactive aqueous phase containing fructose and a chemically modified acid catalyst is contacted with an organic extracting phase modified with a C1-C12 alcohol (preferably 2-butanol).
The method is more commercially viable than those previously developed because it yields a higher concentration of HMF and produces HMF in a separation-friendly solvent which does not require difficult extraction processes. The dehydration process employs a two-phase reactor system in which a reactive aqueous phase containing fructose and a chemically modified acid catalyst is contacted with an organic extracting phase modified with a C1-C12 alcohol (preferably 2-butanol).
Applications
- Synthesizing renewable resources into a precursor for plastics that are usually petroleum-based (PET, PBT, Polyamide/Nylon, Polyester, Polyurethane)
- Biomass-derived precursors for diesel fuel, fuel additives and pharmacologically active compounds
Key Benefits
- Operates at concentrations of fructose between 10 and 50 percent by weight
- Achieves more than 80 percent concentration of HMF with more than 90 percent conversion
- Produces HMF in an easily separable solvent
Stage of Development
Experiments to identify key processing variables for HMF and furfural production using the new method were performed to improve the selectivity of the reaction when using less-reactive molecules. These reactants are desirable because they are inexpensive and abundantly available. Currently, the researchers are producing furfural from corn stover.
Additional Information
Related Intellectual Property
Publications
- Roman-Leshkov Y., Chheda J.N. and Dumesic J.A. 2006. Phase Modifiers Promote Efficient Production of Hydroxymethylfurfural from Fructose. Science. 5782, 1933-1937.
Tech Fields
For current licensing status, please contact Jennifer Gottwald at [javascript protected email address] or 608-960-9854