Clean Technology
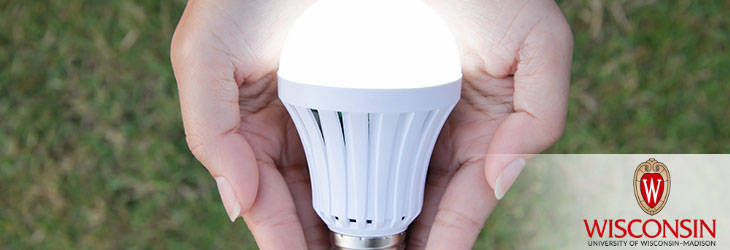
Low-Temperature, Corrosion-Resistant Integrated Metal Coatings to Improve Efficiency of Coal Plants
WARF: P08213US
Inventors: John Perepezko, Ridwan Sakidja
The Wisconsin Alumni Research Foundation (WARF) is seeking commercial partners interested in developing a low-temperature method of synthesizing integrated aluminum coatings for corrosion-resistant metals.
Overview
In 2008, coal-fired power plants generated 49 percent of electricity consumed in the U.S., more than twice that of any other energy resource. Coal is an important fossil fuel because world coal reserves are expected to last about 200 years, much longer than other fossil fuels. However, coal also is a major contributor to atmospheric pollution.
The emissions per unit energy produced from coal-fired power plants are reduced when the efficiency is increased because more energy is captured per unit of coal burned. One way to increase efficiency is to increase the temperature of the combustion chamber, allowing the steam generators to operate near 650°C, the supercritical temperature of steam. Unfortunately, modern chromium/molybdenum/steel alloys produce chromium-based oxides that are not fully protective at temperatures above 550°C. These oxidants lead to the development of scale that tends to spall, causing cross sectional erosion of the steam lines, blockage and degradation of downstream components and overheating.
Protective aluminum coatings, applied via pack cementation, provide resistance to oxidation in high heat and humidity, but two main challenges impede the applicability of this technology. First, prolonged exposure to heat leads to degradation by inward diffusion of the aluminum coating into the steel. More importantly, the high temperature requirement of the pack cementation process leads to degradation of the mechanical properties of the steel alloy. The current method of oxidation protection is not sufficient to allow operation of coal-fired power plants at optimal temperatures.
UW-Madison researchers previously developed a method for applying an oxidation-resistant coating to a molybdenum/silicon/boron alloy. This method involves depositing a diffusion barrier, an oxidation-resistant layer and an oxidation barrier on the alloy substrate (see WARF reference number P03195US). This technique can be used to produce an alloy that supersedes nickel alloys used in high-temperature, high-pressure applications such as turbines and airplane brakes.
The emissions per unit energy produced from coal-fired power plants are reduced when the efficiency is increased because more energy is captured per unit of coal burned. One way to increase efficiency is to increase the temperature of the combustion chamber, allowing the steam generators to operate near 650°C, the supercritical temperature of steam. Unfortunately, modern chromium/molybdenum/steel alloys produce chromium-based oxides that are not fully protective at temperatures above 550°C. These oxidants lead to the development of scale that tends to spall, causing cross sectional erosion of the steam lines, blockage and degradation of downstream components and overheating.
Protective aluminum coatings, applied via pack cementation, provide resistance to oxidation in high heat and humidity, but two main challenges impede the applicability of this technology. First, prolonged exposure to heat leads to degradation by inward diffusion of the aluminum coating into the steel. More importantly, the high temperature requirement of the pack cementation process leads to degradation of the mechanical properties of the steel alloy. The current method of oxidation protection is not sufficient to allow operation of coal-fired power plants at optimal temperatures.
UW-Madison researchers previously developed a method for applying an oxidation-resistant coating to a molybdenum/silicon/boron alloy. This method involves depositing a diffusion barrier, an oxidation-resistant layer and an oxidation barrier on the alloy substrate (see WARF reference number P03195US). This technique can be used to produce an alloy that supersedes nickel alloys used in high-temperature, high-pressure applications such as turbines and airplane brakes.
The Invention
UW-Madison researchers have developed an improved method for the low-temperature synthesis of integrated, corrosion-resistant coatings for metal substrates. The low-temperature process avoids the degradation of substrate mechanical properties that occurs in traditional pack cementation processes. The new method also improves upon previous technologies by widening the scope of its application. For example, synthesis of aluminide coatings on steel alloys via low-temperature pack cementation can enhance oxidation resistance in conditions of extreme temperature and moisture, as in high-temperature operation of steam power generation plants.
In general, the integrated coating consists of the substrate metal, a diffusion-barrier that hinders diffusion of the coating components into the substrate, a corrosion-resistant layer and an oxidation barrier. Deposition of the integrated structure can be achieved via pack cementation at a temperature lower than 700°C, or by thermal spray, vapor deposition or electrodeposition methods.
The substrate, diffusion layer and corrosion-resistant layer can consist of metals, intermetallic compounds or metalloid alloys, depending on the specific application of the integrated structure. For example, a chromium/molybdenum/steel alloy substrate could be coated with an aluminum/iron/intermetallic diffusion-barrier and an aluminum/iron corrosion-resistant layer for use in coal-fired power plants, in which the integrated coating is in contact with supercritical steam. With these techniques, coal-fired power plants can operate at higher temperatures to exploit supercritical steam properties, improving efficiency and reducing overall emissions.
In general, the integrated coating consists of the substrate metal, a diffusion-barrier that hinders diffusion of the coating components into the substrate, a corrosion-resistant layer and an oxidation barrier. Deposition of the integrated structure can be achieved via pack cementation at a temperature lower than 700°C, or by thermal spray, vapor deposition or electrodeposition methods.
The substrate, diffusion layer and corrosion-resistant layer can consist of metals, intermetallic compounds or metalloid alloys, depending on the specific application of the integrated structure. For example, a chromium/molybdenum/steel alloy substrate could be coated with an aluminum/iron/intermetallic diffusion-barrier and an aluminum/iron corrosion-resistant layer for use in coal-fired power plants, in which the integrated coating is in contact with supercritical steam. With these techniques, coal-fired power plants can operate at higher temperatures to exploit supercritical steam properties, improving efficiency and reducing overall emissions.
Applications
- Steam turbine generators in coal-fired power plants
- Heat exchanger components
- Distillation equipment
- Automotive exhaust components
- Chemical reactor tubing
- Refinery tubing
- High-temperature, high-humidity fasteners
Key Benefits
- Improve efficiency and reduce emissions of coal-fired power plants
- Prevents corrosion and oxidation of metal in high-temperature, high-humidity conditions
- Maintains mechanical integrity during coating process
- Applicable to many metal and metal alloy substrates
Additional Information
For More Information About the Inventors
Related Technologies
Publications
- Rioult F., Sekido N., Sakidja R. and Perepezko J. H. 2007. Aluminum Pack Cementation on Mo--Si--B Alloys. Jour. Electrochem. Soc. 154, C692.
Tech Fields
For current licensing status, please contact Emily Bauer at [javascript protected email address] or 608-960-9842