Engineering

Efficient and Automated Analysis of Thin Structures to Enhance Engineering 3-D Modeling Software
WARF: P08425US
Inventors: Krishnan Suresh, Kavous Jorabchi, Josh Danczyk
The Wisconsin Alumni Research Foundation (WARF) is seeking commercial partners interested in licensing technology for efficient and automated analysis of thin structures based on a novel dual representation strategy to enhance 3-D modeling software used by mechanical engineers in computer-aided design.
Overview
Mechanical engineers commonly employ a software modeling tool called finite element analysis (FEA) to virtually simulate a design prior to physical prototyping. In FEA, a three dimensional (3-D) model is broken down into small elements, and element stiffness matrices are assembled to develop a behavioral response of the model. FEA is an integral part of engineering design, and it is usually applied repeatedly until the model is optimized to meet desired performance.
Unfortunately, as is well known, 3-D FEA becomes computationally intractable when analyzing thin structures. Indeed, for thin structures, the common practice is to carry out an explicit geometric reduction in which the 3-D object is reduced to one or two dimensions such as beams, plates or shells before applying FEA. Though well understood, geometric reduction often demands model simplification and expert intervention, which makes implementation difficult and time-consuming.
Unfortunately, as is well known, 3-D FEA becomes computationally intractable when analyzing thin structures. Indeed, for thin structures, the common practice is to carry out an explicit geometric reduction in which the 3-D object is reduced to one or two dimensions such as beams, plates or shells before applying FEA. Though well understood, geometric reduction often demands model simplification and expert intervention, which makes implementation difficult and time-consuming.
The Invention
UW-Madison researchers have developed a new technology for a fully automated and efficient analysis of thin structures. The new process overcomes the limitations of conventional geometric reduction and 3-D FEA by providing a dual-representation, in which the geometry is captured in 3-D, but the physics of the structure are captured via classic beam, plate or shell theory.
The integration of 3-D geometry and lower-dimensional physics leads to numerous advantages:
The integration of 3-D geometry and lower-dimensional physics leads to numerous advantages:
- The technology can be directly integrated into 3-D CAD systems.
- The 3-D CAD model need not be simplified or dimensionally reduced prior to analysis.
- A boundary triangulation of the CAD model is sufficient for analysis, i.e., a 3-D mesh is not required.
- It retains the ability to achieve the accuracy of modern lower-dimensional beam, plate and shell methods.
Applications
- Analysis and optimization of high aspect ratio structures in 3-D CAD environment
- Analysis and optimization of structures with both slender and non-slender components
- Engineering design of aircraft, automobiles, microelectrochemical systems, microfluidic systems, microcantilevers and other microdevices
Key Benefits
- Can be automated and integrated in a shape optimization process
- Can iteratively determine correct reduction process to analyze behavior of element
- Can apply shape optimization to both slender and non-slender elements
- Provides flexibility and generality of 3-D FEA method
- Offers computational efficiency and accuracy of 1-D beam/plate/shell analysis methods
Stage of Development
The iterative technique was used to optimize the shape of a microcantilever. A pilot implementation also is underway; please see the figure for an exemplary screen shot.
The development of this technology was supported by WARF Accelerator. WARF Accelerator selects WARF's most commercially promising technologies and provides expert assistance and funding to enable achievement of commercially significant milestones. WARF believes that these technologies are especially attractive opportunities for licensing.
The development of this technology was supported by WARF Accelerator. WARF Accelerator selects WARF's most commercially promising technologies and provides expert assistance and funding to enable achievement of commercially significant milestones. WARF believes that these technologies are especially attractive opportunities for licensing.
Additional Information
For More Information About the Inventors
Publications
- Mishra V. and Suresh K. 2009. Efficient Analysis of 3-D Plates via Algebraic Reduction. ASME IDETC Conf., San Diego.
Tech Fields
For current licensing status, please contact Emily Bauer at [javascript protected email address] or 608-960-9842
Figures
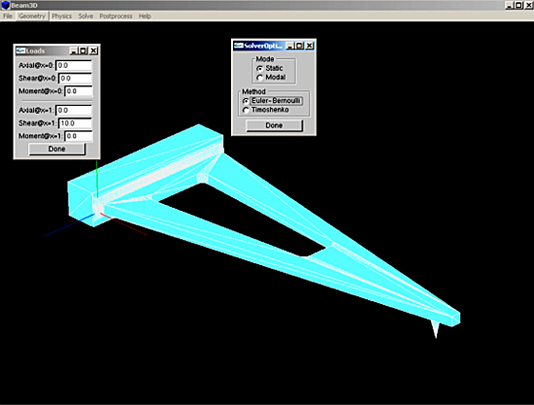