Materials & Chemicals
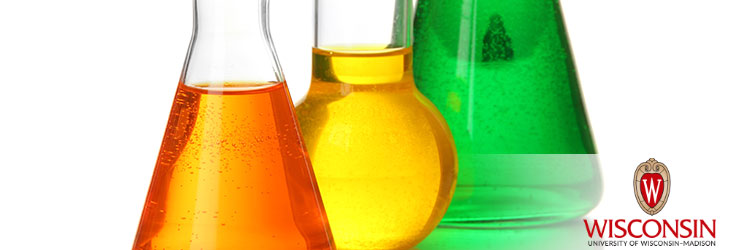
Smoother Plastic Products Using Microcellular Injection Molding
WARF: P110078US01
Inventors: Lih-Sheng Turng, Eugene Dougherty, Chris Lacey, Jungjoo Lee, Pat Gorton, Keith Edgett, Xiaofei Sun
The Wisconsin Alumni Research Foundation (WARF) is seeking commercial partners interested in improving a technique for manufacturing feminine hygiene products and other high-quality personal and consumer plastics.
Overview
Several techniques exist for turning plastic into goods and packaging. Microcellular foams are of particular interest because they can be used to produce strong, lightweight plastic. Unfortunately, during the molding process, gases from the foam can escape from the plastic and cause swirling patterns or gritty texture on the part surface, resulting in rough and unappealing products.
Given these drawbacks, measures have been taken to improve the surface quality of parts formed by microcellular injection molding. These measures have proven costly and often require complicated mold redesigns and operation.
Given these drawbacks, measures have been taken to improve the surface quality of parts formed by microcellular injection molding. These measures have proven costly and often require complicated mold redesigns and operation.
The Invention
UW–Madison researchers and others have improved the microcellular injection molding process to create smoother plastic parts.
In the new process, a polymer is heated, melted and mixed with a low amount of supercritical fluid (such as nitrogen). The resulting mixture is a single-phase solution. The polymer and/or the supercritical fluid may be adjusted to control the weight of the component or its surface properties. Once adjusted, the mixture is injected into a mold. Proper control of the supercritical fluid content in the polymer causes bubbles in the polymer to nucleate in a controlled fashion, which leads to products with a much smoother surface.
In the new process, a polymer is heated, melted and mixed with a low amount of supercritical fluid (such as nitrogen). The resulting mixture is a single-phase solution. The polymer and/or the supercritical fluid may be adjusted to control the weight of the component or its surface properties. Once adjusted, the mixture is injected into a mold. Proper control of the supercritical fluid content in the polymer causes bubbles in the polymer to nucleate in a controlled fashion, which leads to products with a much smoother surface.
Applications
- Microcellular foam injection molding
- Manufacturing a wide array of high-volume, high-quality parts like tampon applicators
Key Benefits
- Improves surface and mechanical qualities
- Reduces gritty texture and swirling
- Cuts raw materials and overall cost of products
- Can be implemented in existing molds
- Enables manufacturing with a variety of polymer resins
- Lower temperature and clamp pressure levels promote higher productivity and faster cooling times.
Additional Information
Related Technologies
Tech Fields
For current licensing status, please contact Michael Carey at [javascript protected email address] or 608-960-9867