Materials & Chemicals
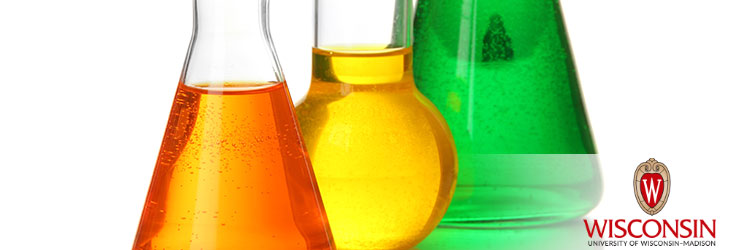
Highly Foamed Plastic Parts Are Stronger and Cheaper to Produce
WARF: P130051US01
Inventors: Lih-Sheng Turng, Xiaofei Sun
The Wisconsin Alumni Research Foundation (WARF) is seeking commercial partners interested in developing a method for fabricating foamed, injection-molded components with better surface quality and lower weight.
Overview
Microcellular injection molding produces lightweight, dimensionally stable plastic components using fewer raw materials than standard techniques.
The process, also known as ‘microcellular foaming,’ mixes a supercritical fluid into a polymer melt prior to injecting the polymer into a mold. The polymer solidifies in the mold to form a desired component with complex geometry. The supercritical fluid causes tiny bubbles to be distributed throughout the mold. As a result of the bubbles, less raw material is necessary to mold the component while dimensional stability is improved. The foam expansion allows the removal of the packing stage from the injection molding cycle and also leads to a shortened cooling stage, which saves the total cycle time significantly.
Unfortunately, microcellular foaming can require expensive, specialized equipment. Major modifications to the injection molding machine design and control system are required, and can only be done by the machine supplier. Also, the surfaces of components tend to be irregular or rough. A better technique should be cost-effective and ensure good production rates.
The process, also known as ‘microcellular foaming,’ mixes a supercritical fluid into a polymer melt prior to injecting the polymer into a mold. The polymer solidifies in the mold to form a desired component with complex geometry. The supercritical fluid causes tiny bubbles to be distributed throughout the mold. As a result of the bubbles, less raw material is necessary to mold the component while dimensional stability is improved. The foam expansion allows the removal of the packing stage from the injection molding cycle and also leads to a shortened cooling stage, which saves the total cycle time significantly.
Unfortunately, microcellular foaming can require expensive, specialized equipment. Major modifications to the injection molding machine design and control system are required, and can only be done by the machine supplier. Also, the surfaces of components tend to be irregular or rough. A better technique should be cost-effective and ensure good production rates.
The Invention
UW–Madison researchers have developed a new method of fabricating highly foamed, injection-molded plastic parts. Firstly, a thermoplastic material like LDPE is heated along with supercritical nitrogen or carbon dioxide to produce a gas-polymer solution in an extruder, and then the melt is extruded and quenched into gas-laden pellets. These pellets are plasticized in an injection molding machine, and then injected into a mold to produce lightweight parts with fine foamed structure and/or improved part surface.
Compared with the conventional method, this method requires much lower equipment cost and process complexity, no modification to the injection molding machines is needed, and all the same benefits that the conventional method offers can be achieved.
Compared with the conventional method, this method requires much lower equipment cost and process complexity, no modification to the injection molding machines is needed, and all the same benefits that the conventional method offers can be achieved.
Applications
- Producing lightweight, high-quality plastic parts like auto, transportation, personal care items and packaging
Key Benefits
- Components have smaller, denser bubbles.
- Cuts costs
- Improves surface finish
- Method is simple and can be used with standard machinery.
- Eliminates the need for chemical blowing agents, which have safety and quality concerns
Additional Information
Related Technologies
Publications
- Sun X. and Turng L.S. 2013. Novel Injection Molding Foaming Approaches Using Gas-Laden Pellets with N2, CO2, and N2 + CO2 as the Blowing Agents. Polym. Eng. and Sci. [Epub]
- Lee J., Turng L.S., Dougherty E. and Gorton P. 2011. Novel Foam Injection Molding Technology Using CO2-Laden Pellets. Polym. Eng. and Sci. 51, 2295-2303.
Tech Fields
For current licensing status, please contact Michael Carey at [javascript protected email address] or 608-960-9867