Clean Technology
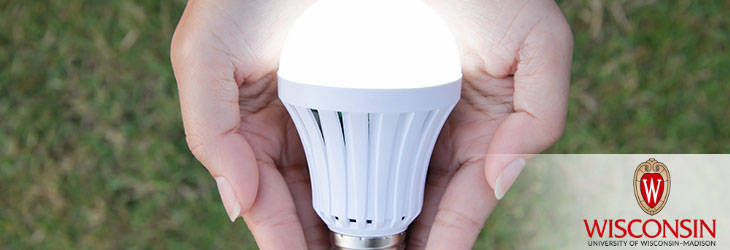
Using Power Plant & Industrial Wastes to Sequester CO2 into High Purity Products
WARF: P200242US02
Inventors: Bu Wang, Raghavendra Ragipani
The Wisconsin Alumni Research Foundation is seeking commercial partners interested in developing a method to convert carbon dioxide and industrial wastes such as fly ash from power plants or slag from steel mills into calcium carbonate and other products that may be sold to various industries and used for carbon credits.
Overview
In the U.S., coal plants produce around 50 million tons of waste each year that is rich in calcium, magnesium and other elements but is landfilled at a cost of $3-35/ton. Similarly, an estimated two billion tons of fly ash and slag (the byproducts of metal smelting) is currently stored in U.S. repositories. Globally, more than 360 million tons of fly ash is produced each year, with India, China, the U.S. and Germany having the highest shares. Many of these waste streams exist side-by-side with CO2 flue gas streams, where federal tax credits provide a financial incentive to sequester CO2.
Existing CO2 sequestration technologies that make use of these industrial wastes typically require energy-intensive particulate grinding or high temperatures and pressures to increase reaction rates to reasonable time scales. These complications make the entire process financially infeasible.
Existing CO2 sequestration technologies that make use of these industrial wastes typically require energy-intensive particulate grinding or high temperatures and pressures to increase reaction rates to reasonable time scales. These complications make the entire process financially infeasible.
The Invention
UW-Madison researchers have developed a multistep process to sequester CO2 using industrial wastes from coal plants or metal foundries. This process has fast reaction times, is more economical and uses less energy. It can take place at ambient temperatures and pressures, with conversion efficiencies of oxides into carbonates up to ~80% within 1 hour and ~95% within 24 hours. In addition, the process is regenerative, works best in an alkaline environment and may be paired with direct air capture of dilute CO2 streams.
Applications
- Metal foundries and power plants (coal) can spend less money landfilling waste and generate additional revenue streams from their waste products.
- The Precipitated Calcium Carbonate (PCC) that may be produced from this process is used in the paper, adhesives and plastics industry.
- May be paired with a direct air capture technology to dilute CO2 streams for carbon credits
Key Benefits
- One of the only processes to use the CaO and Al2O3 silicates found in fly ash, which make up 30-50% of the oxides by mass
- Works at ambient pressures and can work at ambient temperatures
- Relies on thermodynamically favorable processes for low energy input ~30% cheaper than other direct air capture carbon sequestration processes
Stage of Development
This process has been tested with fly ash from the Weston Power Plant in Kronenwetter, Wisconsin. There was a reported near 100% conversion efficiency from the calcium in the fly ash into calcium carbonate.
The development of this technology was supported by WARF Accelerator. WARF Accelerator selects WARF's most commercially promising technologies and provides expert assistance and funding to enable achievement of commercially significant milestones. WARF believes that these technologies are especially attractive opportunities for licensing.
The development of this technology was supported by WARF Accelerator. WARF Accelerator selects WARF's most commercially promising technologies and provides expert assistance and funding to enable achievement of commercially significant milestones. WARF believes that these technologies are especially attractive opportunities for licensing.
Additional Information
For More Information About the Inventors
For current licensing status, please contact Michael Carey at [javascript protected email address] or 608-960-9867