Materials & Chemicals
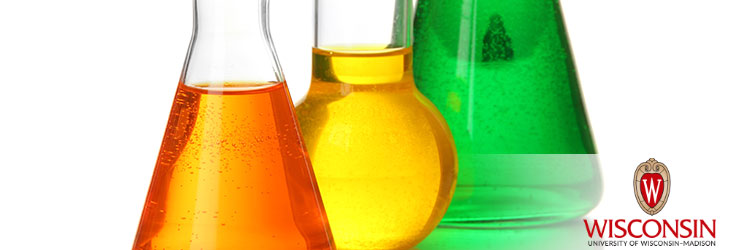
Bio-Composite Materials For 3D Printing Using Milk Proteins
WiSys: T200060US02
Inventors: John Obielodan, Joseph Wu
WiSys is seeking a strategic partner in the 3D printing industry who can provide a route to market for the commercialization and use of these bio-composite milk protein printing materials. There is also interest in identifying an industry partner to assist in further optimization of the formulation and properties of these bio-composites
Overview
Recent global estimates project that over 125 million tons of dairy products are wasted or discarded due to spoilage each year. Roughly half of this waste occurs before the products even reach the consumer. Milk is composed of 3.5% protein, of which casein and whey are the two major protein compounds. To date, both proteins have been explored as useful biopolymers. With the staggering amount of casein and whey that is discarded annually, there exists an opportunity to find high value uses for these compounds.
The 3D printing market continues to grow at a significant rate globally. A BCC Research market report estimates that the global market for 3D printing will reach just under $14 billion in 2024. Within this market, the material extrusion printing technology holds the largest share projected to reach $5.2 billion in 2024, followed by VAT photopolymerization estimated to reach $3.2 billion. Material extrusion is low-cost and uses thermoplastic filaments as the printing material. Common thermoplastics used in 3D printing are ABS (acrylonitrile butadiene styrene) and PLA (polylactic acid). ABS is a petroleum derived plastic that has high strength, flexibility, and durability, but is prone to warping during printing and is not biodegradable. In contrast, PLA is made from environmentally friendly renewable resources, but it has been found to be brittle. Recent efforts to overcome these deficiencies have been explored through the development of bio-composite polymers using PLA and another biodegradable, eco-friendly material. Promising results invite opportunity to identify additional materials that can be combined with PLA for an enhanced printing filament.
The Invention
Two researchers from the University of Wisconsin – Platteville have developed a 3D printing bio-composite material made of PLA and the milk protein casein. Preliminary tests with specimens printed using this bio-composite material show elasticity, tensile strength, and impact strength measurements comparable with specimens printed using PLA alone. Additionally, these researchers have developed a resin containing casein for use in VAT photopolymerization 3D printing. Printed samples generated from this bio-composite resin showed elasticity and tensile strength measurements comparable with samples printed using a standard photopolymer resin. Optimization and further testing of these bio-composite materials is ongoing. Furthermore, development of similar bio-composite materials with the milk protein whey is in progress.
Key Benefits
- High value use for proteins in milk waste
- Reduces the environmental impact and financial losses resulting from dairy waste
- Fully biodegradable 3D printing filament: casein from milk waste and plant-derived PLA
- Enhanced biodegradable properties of photopolymer resin with added casein
- Physical properties of printed objects align with industry standard printing materials
- Extraction and recovery of casein and whey from spoiled milk is easier than generating PLA
- Reduced material cost
Stage of Development
A 3D printing bio-composite material made of PLA and the milk protein casein has been developed. Additionally, these researchers have developed a resin containing casein for use in VAT photopolymerization 3D printing. Optimization and further testing of these bio-composite materials is ongoing. Furthermore, development of similar bio-composite materials with the milk protein whey is in progress.
Tech Fields
For current licensing status, please contact Jennifer Souter at [javascript protected email address] or (608) 316-4131